Why a Welding WPS is Crucial: Enhancing Uniformity and Conformity
Why a Welding WPS is Crucial: Enhancing Uniformity and Conformity
Blog Article
Grasping Welding WPS Specifications: Ideal Practices and Techniques for Top Quality Welds
In the world of welding, understanding Welding Procedure Requirements (WPS) standards is a vital component that directly affects the high quality and stability of welds. As we browse through the details of welding WPS criteria, uncovering crucial understandings and techniques for accomplishing top-tier welds will certainly be paramount for welders seeking to excel in their craft and generate welds that stand the test of time.
Comprehending Welding WPS Requirements
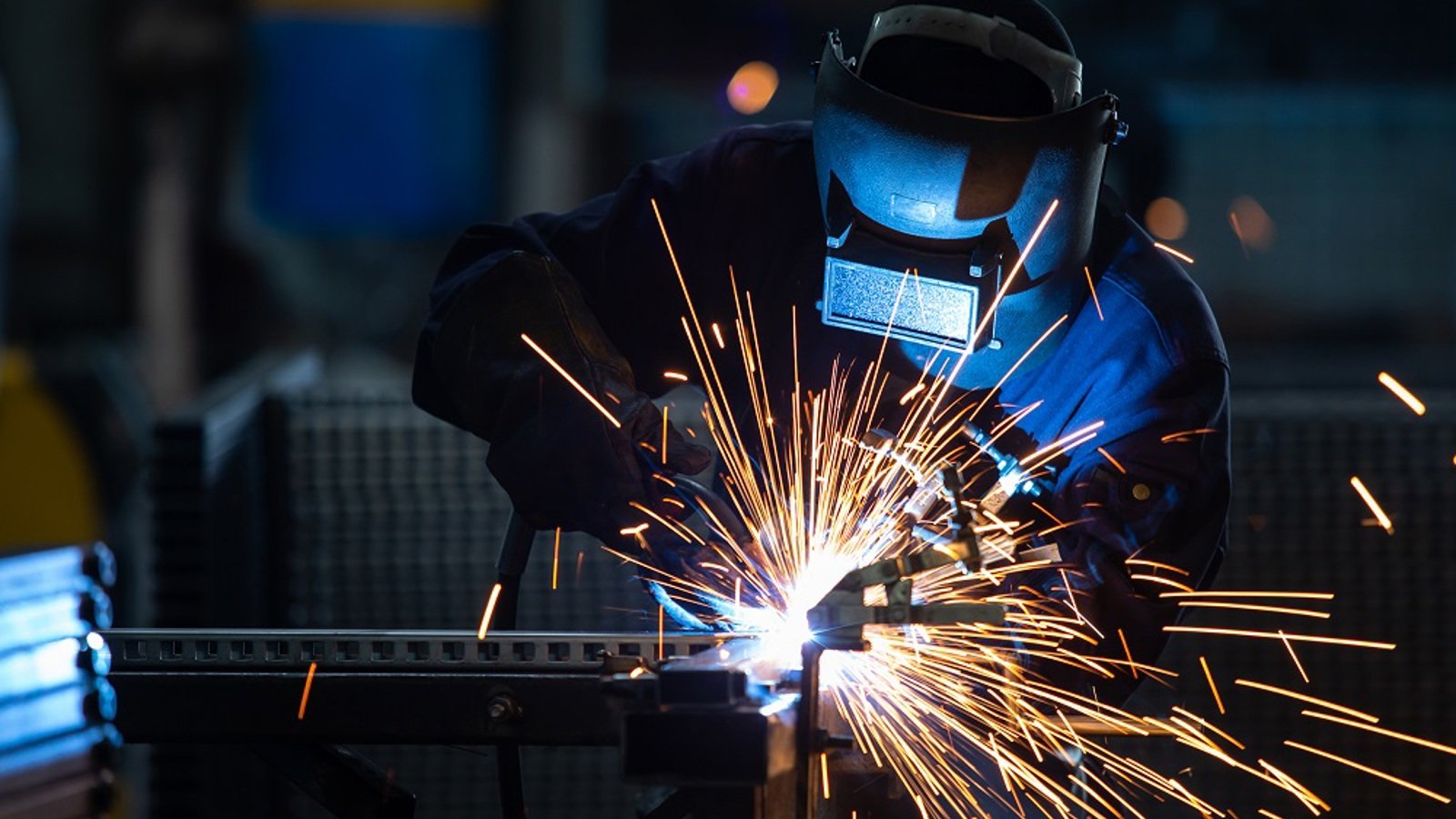
Examiners depend on WPS documentation to verify that welding treatments are being adhered to properly and that the resulting welds are of high quality. Designers use WPS standards to make welding treatments that guarantee the sturdiness and dependability of welded frameworks.
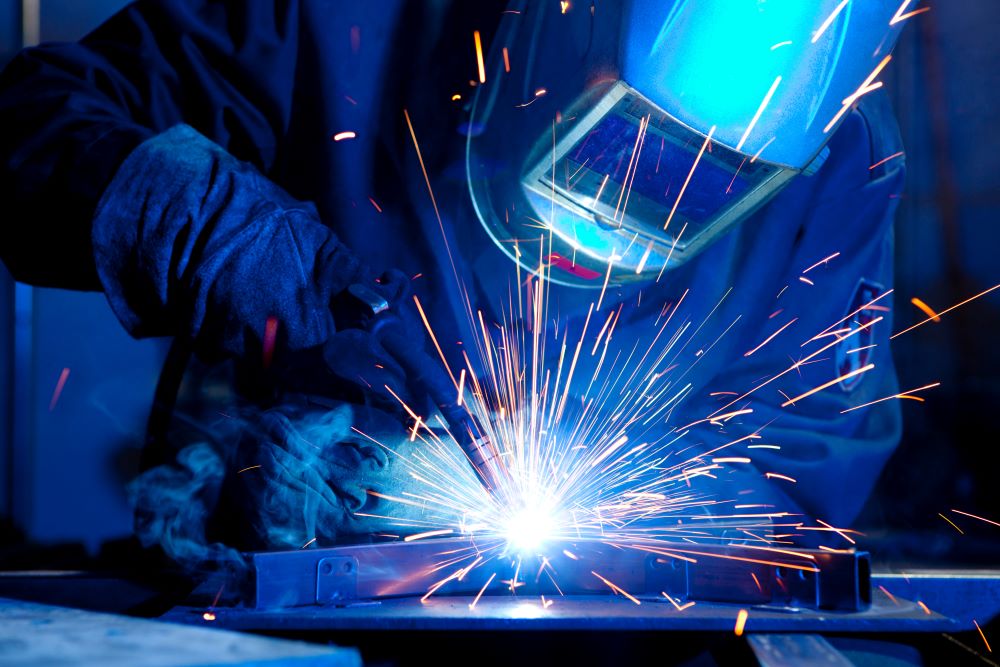

Important Tools for High Quality Welds
Mastering welding WPS requirements is important for welders to properly make use of the crucial devices needed for producing quality welds. Among one of the most vital tools for high quality welds is a welding equipment. The sort of welding equipment required relies on the welding procedure being used, such as MIG, TIG, or stick welding. Welding safety helmets are likewise important to protect the welder's eyes and face from stimulates, heat, and UV radiation. Furthermore, welding gloves constructed from long lasting and heat-resistant products secure the hands from injuries and burns. Magnets and clamps aid hold the work surfaces with each other securely throughout the welding process, making sure exact and accurate welds. Cord brushes and cracking hammers are important for cleaning the weld joint prior to and after welding to get rid of any kind of contaminations that might impact the high quality of the weld. Last but not least, a gauging tape and angle grinder serve tools for making certain proper positioning and preparing the work surfaces for welding.
Key Techniques for Welding Success
To attain welding success, one have to understand the crucial techniques necessary for creating high-grade welds. One essential technique is preserving the appropriate arc length. Maintaining the electrode at the optimum distance from the workpiece is read this article important for developing strong, uniform welds. In addition, regulating the traveling rate is critical. Moving as well rapidly can lead to inadequate penetration, while moving as well gradually can result in extreme warmth input and possible issues. Proper control of the electrode angle is one more essential method. The angle at which the electrode is held can impact the bead shape and infiltration of the weld. In addition, ensuring constant weapon angle and direction of travel is crucial for uniformity in the weld bead. Finally, keeping a constant hand and a her comment is here steady welding position throughout the process is essential to accomplishing precision and consistency in the welds. By understanding these essential methods, welders can boost the quality of their work and attain welding success.
Ensuring Compliance With WPS Standards
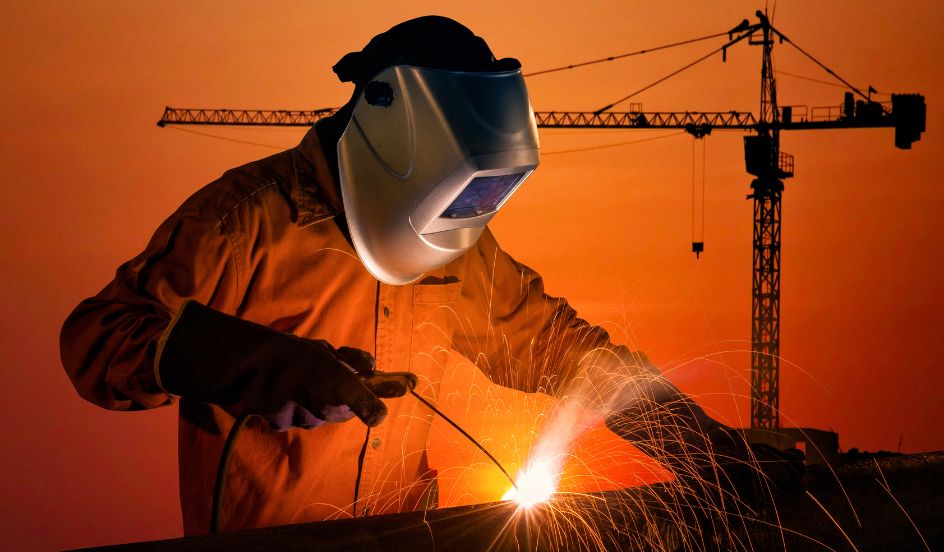
Furthermore, keeping comprehensive documents of welding specifications, equipment calibration, and inspection outcomes is crucial for demonstrating conformity with WPS requirements. By carefully sticking to WPS standards, welders can make certain that their work satisfies the needed top quality degrees and adds to the general success of the welding task.
Troubleshooting Common Welding Issues
When encountered with usual welding concerns, identifying the source is critical for efficient troubleshooting. One widespread problem is the existence of porosity in welds, typically triggered by impurities such as corrosion, dampness, or oil. To resolve this, guaranteeing appropriate cleaning of the base steel prior to welding and using the proper securing gas can dramatically decrease porosity. One more issue frequently encountered is absence of fusion, where the weld falls short to properly bond with the base material. This can originate from inadequate heat input or incorrect welding method. Changing parameters such as voltage, cord feed rate, or travel speed can help enhance combination. Additionally, distortion, cracking, and spatter are common welding difficulties that can be mitigated with proper joint preparation, constant heat control, and picking the proper welding consumables. By completely comprehending these typical welding issues and their origin, welders can effectively fix troubles and accomplish high-grade welds.
Verdict
In conclusion, grasping welding WPS standards calls for a comprehensive understanding of the standards, using essential tools, and executing crucial techniques for effective welds. Making sure you can check here compliance with WPS requirements is critical for creating top quality welds and staying clear of typical welding issues. By adhering to ideal techniques and methods, welders can achieve regular and trusted lead to their welding jobs.
In the realm of welding, mastering Welding Procedure Requirements (WPS) criteria is a crucial element that straight influences the quality and stability of welds.When diving into the world of welding practices, a crucial aspect to comprehend is the importance and ins and outs of Welding Treatment Requirements (WPS) criteria. WPS criteria offer a detailed guideline for welding operations, ensuring uniformity, high quality, and safety in the welding procedure. The kind of welding equipment needed depends on the welding process being used, such as MIG, TIG, or stick welding.Accomplishing welding success through the mastery of key techniques requires a detailed understanding and adherence to Welding Procedure Requirements (WPS) criteria.
Report this page